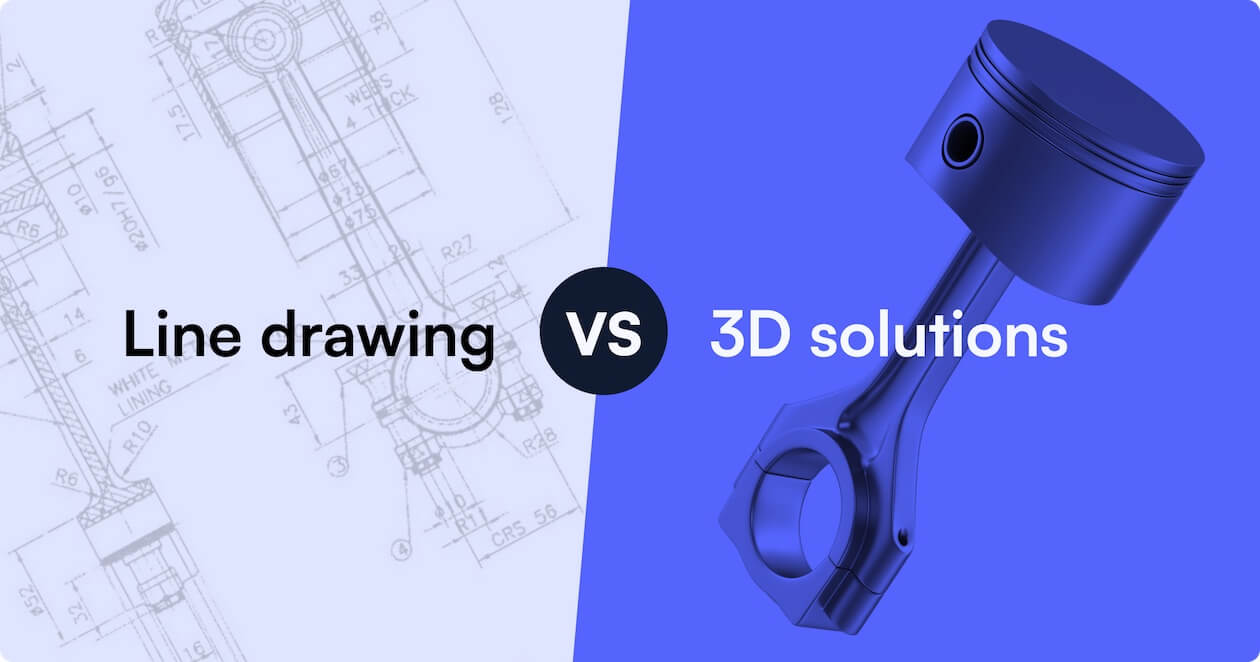
Does the true value of prototyping come from exploiting the strengths of both physical and digital methods?
We discussed this concept with a leading professional services firm, The Design Technology Company (DTCo.). They provide cutting edge mechanical designs and prototypes to a wide range of engineering and manufacturing clients.
We discuss the fact that a hybrid solution could resolve more unknowns in the product development process earlier. In turn, reducing the need for future design iterations, or worse, getting it completely wrong in the first place…
This is the first article in our expert series with DTCo.
The Evolution of Prototyping: From Physical to Digital
Rapid prototyping is supercharging product development, bridging the gap between concept and reality with unprecedented speed and efficiency. As digital technologies evolve, so does the prototyping landscape, seamlessly blending the tactile power of physical models with the agility of digital iterations. It’s a dynamic fusion reshaping how innovators tackle design validation and iteration, pushing the boundaries of what's possible. Let's dive into the world of digital and physical prototypes, and uncover where the true value lies in this game-changing process.
Traditionally, prototyping meant creating physical models to test and refine product designs. However, the advent of advanced 3D modelling software and virtual reality has introduced a new player: digital prototyping. This shift has revolutionized the way companies approach product development, offering new possibilities and efficiencies.
What is the purpose of prototyping?
A prototype is often required to validate the accuracy of a product being created and to garner feedback. Essentially, it is a draft design for validation.
There are various reasons and purposes for creating a product prototype, which can include a combination of:
- Accuracy: You might build on to explore how a mechanism functions in reality. Parameters like friction can be notoriously difficult to determine theoretically, a prototype allows the theoretical estimates to be verified empirically.
- Ergonomics: It is nearly impossible to determine how a physical object will 'feel' to touch, hold or use without physically producing it. Prototypes with limited functionality can be built to resolve this unknown
- Aesthetics: A prototype can help you define the colors, textures and materials needed.
- Survey: You can survey people to get feedback, gather information and validate a product within an audience. Or you may be trying to measure reactions to a product when people see it.
- Pitch: Used to determine if you can share an idea with someone to raise funds.
- Testing: Used to validate mechanical elements of a design and determine what tweaks are required. Often used in conjunction with accuracy, if the prototype works.
The power of physical prototypes
Physical prototypes have long been the gold standard in product development, and for good reason:
- Tactile Feedback: Nothing beats the ability to hold, feel, and interact with a physical prototype. This is crucial for evaluating ergonomics and user experience.
- Functional Testing: Physical prototypes allow for real-world testing of mechanisms, durability, and performance under actual conditions.
- Material Validation: They provide an opportunity to test and validate material choices, finishes, and textures.
- Stakeholder Engagement: Physical prototypes can be powerful tools for engaging stakeholders, from investors to potential customers. In fact, usingAR to pitch investors can take this engagement to the next level.
The power and rise of digital prototypes
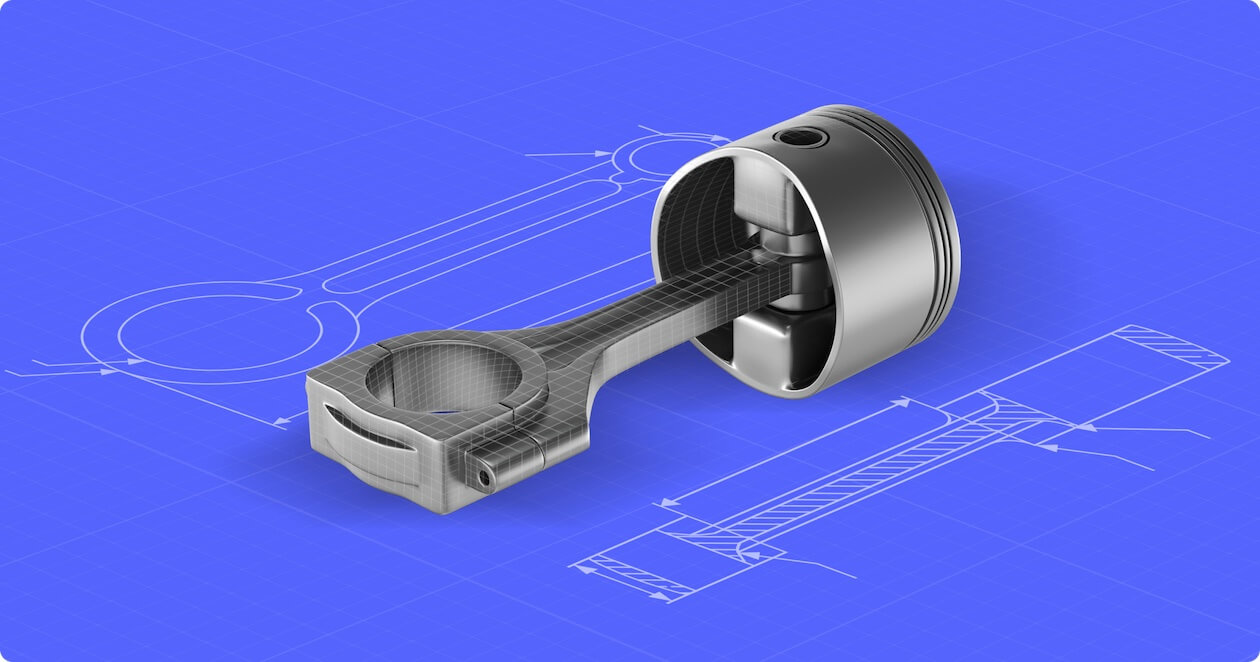
Prototyping usually means moving out of the conception and analytical space into the physical world. Digital (or virtual) prototypes challenge this physical presence as the status quo.
Digital prototypes can be used to enhance many of the following design stages:
- Survey and Research: If the intention is to determine which design is preferred (from multiple choices), delivering a product in the digital world can garner results quicker and at scale vs physically building an example. This digital enablement can also lower the cost of running physical focus groups while providing more data points.
- Aesthetics: Validating aesthetic desire and appeal for a product can be made easier and more accessible by enabling digital examples.
- Pitch and Sales: Sharing design ideas with investors and customer prospects in a digital format already exists within the use of 2D line drawings, pitch decks, videos, and imagery. The utilization of interactive 3D models can bring complex concepts into a far more engaging and lifelike storyboard to demonstrate.
- User trial and orientation: Users can simulate the usage of the product and see its different orientations in space.
Digital prototyping is unlikely to replace all stages of the process such as accuracy, ergonomics and testing.
Good digital prototypes surface benefits that the constraints of a CAD system do not allow. Benefits such as shareability, deployability, and accessibility in an aesthetically pleasing way.
JigSpace takes this one step further by allowing engagement with the prototype through augmented reality and the ability to interact in a lightweight web AR viewer.
Quick overview of the benefits of digital prototyping
- Speed and Iteration: Digital prototypes can be created and modified much faster than physical ones, allowing for rapid iteration and refinement.
- Cost-Effective: Without the need for materials or manufacturing processes, digital prototyping can significantly reduce costs, especially in the early stages of development.
- Visualization: Advanced rendering techniques allow for photorealistic visualizations of products before they're physically created.
- Collaboration: Digital prototypes can be easily shared and collaborated on across teams and locations.
- Integration with Simulations: Digital models can be integrated with various simulation tools to test performance, stress, and other factors virtually.
Enter Rapid Prototyping
While physical prototypes excel in providing tangible insights into ergonomics and functionality, and digital prototypes shine in enabling quick iterations and broad accessibility, the true strength of modern prototyping lies in approaches that combine both. This is where rapid prototyping comes into play, acting as a bridge between these two worlds.
By leveraging technologies like 3D printing, rapid prototyping transforms digital concepts into physical forms at unprecedented speed, maintaining the precision and flexibility of virtual models while offering the hands-on benefits of tangible prototypes. This blended process not only accelerates design validation but also enhances the efficiency of the overall development cycle, making it an indispensable tool in today’s prototyping landscape.
What is Rapid Prototyping?
Rapid prototyping is a group of techniques used to quickly fabricate a scale model of a physical part or assembly using three-dimensional computer aided design (CAD) data. While it often refers to 3D printing technologies, the term encompasses a broader range of processes that can quickly create prototype parts.
These days the quick print physical forms are often referred to as ‘rapid prototypes’. They are commonly 3D printed objects that assist with evaluating ergonomics i.e. “how does this feel in my hand?”.
Rapid prototypes turn out a rough form of an end part, or close to it. From there it is easy to determine how much space the object requires, how it feels, and how it fits within an environment.
Digital/virtual can enhance rapid prototypes
The Prado Boot Bar Part - Created by DTCo.
The Hybrid Approach: Combining Digital and Physical Prototyping
While both digital and physical prototyping have their strengths, the real power lies in combining these approaches. This hybrid method allows teams to leverage the speed and flexibility of digital prototyping with the tangible benefits of physical models.
Jonathan Bannister, Managing Director at The Design Technology Company (DTCo.), a leading professional services firm specializing in mechanical designs and prototypes, emphasizes this point:
"Digital prototyping enables rapid feedback on some design factors, this feedback advances the design maturity of the physical prototype that follows, enhancing its effectiveness and shortening the design process"
This approach allows teams to:
- Refine Designs Quickly: Use digital prototyping for rapid iterations and refinements.
- Validate Virtually: Conduct initial validations and simulations digitally.
- Create Targeted Physical Prototypes: Use insights from digital prototypes to create more refined and purposeful physical prototypes.
- Enhance Presentation: Utilize both digital and physical prototypes for comprehensive stakeholder presentations, especially when augmented reality for technical sales comes into play.
Digital, virtual and AR prototypes are unlikely to replace physical ones across the ENTIRE spectrum of the design process. However, most durable manufacturing and engineering businesses still create ONLY 2D imagery and physical prototypes across their prototyping journey.
Digital options can be far more impactful in many circumstances, as the coordination of the physical options can be at an epic scale of time and cost. There is certainly room for a hybrid method to replace the traditional.
It is great to see innovative companies like DTCo. leading the way and disrupting the process, using JigSpace as some of the cornerstone technology to achieve this.
The 3 approaches to prototyping simplified
Traditional Prototyping:
- Physical models: Tangible representations you can touch and feel.
- Functional prototypes: Working models that bring your ideas to life.
- Material testing: Get hands-on with the real stuff.
Digital Prototyping:
- CAD models: Precision digital designs that let you tweak every last detail.
- Virtual simulations: Test your product in a digital playground.
- Interactive UIs: Click, swipe, and interact with your digital products.
And here's where the magic happens - the Hybrid Approaches:
- 3D printing: Turn pixels into tangible objects in hours.
- AR/VR experiences: Immerse yourself in your product before it exists.
- Digital twins: Create virtual replicas for real-time optimization.
Leveraging Advanced Technologies in Prototyping
The prototyping landscape is continuously evolving with the integration of advanced technologies:
Augmented Reality (AR) in Prototyping
AR technologies, like those offered by JigSpace, are bridging the gap between digital and physical prototyping. They allow users to:
- Visualize digital prototypes in real-world contexts
- Interact with virtual models as if they were physical objects
- Share and collaborate on prototypes remotely
This technology is particularly powerful when it comes to augmented reality for product training, allowing teams to familiarize themselves with new products before they're even manufactured.
Data-Driven Prototyping
The integration of data analytics in the prototyping process is leading to more informed design decisions. This data prototyping approach allows teams to:
- Analyze user interactions with digital prototypes
- Gather quantitative feedback on design iterations
- Make data-driven decisions throughout the development process
The Future of Rapid Prototyping
As technology continues to advance, the lines between digital and physical prototyping will likely blur further. We can expect to see:
- More Realistic Digital Prototypes: With advancements in VR and haptic feedback, digital prototypes will become increasingly lifelike.
- Faster Physical Prototyping: Improvements in 3D printing and other rapid manufacturing techniques will speed up the creation of physical prototypes.
- AI-Assisted Design: Artificial intelligence will play a larger role in generating and optimizing prototype designs.
- Enhanced Simulation Capabilities: More sophisticated simulation tools will allow for even more accurate virtual testing.
Conclusion: The Value of a Balanced Approach
While digital prototyping has revolutionized the product development process, it's clear that physical prototypes still hold immense value. The true power lies in leveraging both approaches strategically throughout the development cycle.
By embracing a hybrid approach to rapid prototyping, companies can:
- Reduce development time and costs
- Improve product quality and user experience
- Enhance communication with stakeholders
- Stay competitive in a fast-paced market
As we move forward, the most successful product development teams will be those that can seamlessly integrate digital and physical prototyping methods, leveraging the strengths of each to create innovative, user-centric products.
Are you ready to revolutionize your prototyping process? Explore how JigSpace can enhance your digital prototyping capabilities and bridge the gap between virtual and physical product development. From augmented reality for product collateral to immersive training experiences, the possibilities are endless.
FAQs
How does rapid prototyping differ from traditional prototyping methods?
Traditional prototyping often involves manual, time-intensive processes, leading to higher costs and limited flexibility. Rapid prototyping, on the other hand, employs digital tools and automated manufacturing methods, allowing for faster production, more iterations, and the ability to make design changes quickly and cost-effectively.
What is the role of digital prototyping in the design process?
Digital prototyping allows designers to create virtual simulations of a product using tools like CAD or 3D modelling software. This process supports testing and refinement of designs in a cost-efficient and timely manner while providing critical insights before physical production begins.
How does physical prototyping complement digital prototyping?
While digital prototyping is ideal for evaluating design and functionality in a virtual space, physical prototyping enables tactile testing and validation of a product. Combining the two approaches ensures comprehensive feedback, addressing both visual and functional aspects of a design.
What are some common examples of rapid prototyping technologies?
Common rapid prototyping technologies include 3D printing methods such as SLA, SLS, and FDM, as well as CNC machining, vacuum casting, and binder jetting. These technologies allow for the efficient creation of prototypes with varying levels of precision and functionality.
Which industries commonly use rapid prototyping?
Rapid prototyping is widely used across industries such as automotive, aerospace, healthcare, consumer goods, and electronics. It supports fast development of new products by enabling early testing of designs and functionality in applications like car components, medical devices, and consumer appliances.
Does a prototype have to be physical?
No, prototypes can be either physical or digital. While physical prototypes provide tangible insights and allow hands-on testing, digital prototypes offer virtual simulations for validating designs early in the process. Both types are valuable, depending on the development stage and project goals.
How does virtual prototyping compare to physical prototyping?
Virtual prototyping focuses on simulating a product’s design and functionality in a digital environment, offering benefits like cost efficiency and quick modifications. Physical prototyping, however, validates the tactile and ergonomic aspects of a product. Together, these approaches ensure thorough testing and refinement.
What is the difference between a prototype and a model?
A prototype is a functional representation of a product designed for testing usability, functionality, or design elements. A model, however, is typically a non-functional representation used for visualization or demonstration purposes, such as for presentations or marketing materials.
Can rapid prototyping be used to prototype textures and aesthetics?
Yes, rapid prototyping technologies, like SLA or multi-material 3D printing, can create detailed aesthetic representations, including textures and finishes. This makes it possible to evaluate and refine the visual and tactile qualities of a product prior to manufacturing.
What is the definition of virtual prototyping?
Virtual prototyping is the creation of interactive, digital simulations of a product using software tools. It allows for the testing of design, functionality, and usability in a virtual environment, reducing the need for physical prototypes during the early stages of development.
What is a digital prototyping service?
A digital prototyping service provides tools and expertise to design, simulate, and test virtual prototypes of products. These services often include CAD modelling, 3D visualization, and simulation support, helping businesses refine their concepts before transitioning to physical production.
What is the value of combining digital and physical prototyping?
Combining digital and physical prototyping leverages the strengths of both methods. Digital prototypes enable quick ideation and modifications, while physical prototypes provide tangible validation for ergonomics and functionality. Together, they reduce costs, shorten development cycles, and improve design accuracy.
What challenges can arise in the rapid prototyping process?
While rapid prototyping offers numerous advantages, several challenges can arise during the process. These include:
- Material selection issues: Not all materials used in prototyping closely mimic the properties of final production materials, which can impact testing accuracy.
- Design complexity limits: Some rapid prototyping technologies have restrictions on size, complexity, or detail.
- Cost management: Although faster than traditional methods, creating multiple iterations can still lead to higher costs if not managed properly.
- Over-reliance on prototypes: Teams may focus too heavily on refining prototypes rather than addressing broader design or production issues.
- Technology limitations: Rapid prototyping depends on advanced equipment and software, which might not always be accessible or available to all teams.
What factors affect the speed of the rapid prototyping process?
Several factors influence the speed of the rapid prototyping process, including:
- Technology used: The type of rapid prototyping technology, such as 3D printing (SLA, FDM, SLS) or CNC machining, significantly affects speed. For instance, additive manufacturing methods like FDM are generally faster than CNC machining but may compromise precision in complex designs.
- Design complexity: Highly detailed or intricate designs take longer to prototype due to increased processing time for modeling and building the prototype.
- Material choice: Certain materials require different processing times. For example, durable metals might take longer to process compared to lightweight polymers or resins.
- Iteration cycles: The number of iterations required for testing and refining designs also impacts the overall speed, as each cycle involves processing and feedback integration.
- Software and automation: Tools with advanced features like AI-driven optimization or cloud-based collaboration significantly reduce prototyping time through real-time adjustments and streamlined workflows.
Efficient use of these factors can drastically shorten the development timeline while maintaining design accuracy and functionality.
Are there software tools to enhance rapid prototyping efficiency?
Yes, there are multiple software tools designed to enhance the efficiency of rapid prototyping. These tools support various aspects of the prototyping process, from design and modeling to collaboration and testing. Some of the most widely used software tools are:
- CAD software: Tools like OnShape, SolidWorks, and Shapr3D offer features for creating precise 3D models that can be used for digital and physical prototypes.
- Prototyping platforms: Software like Figma and Axure RP enable the creation of interactive digital prototypes or wireframes for testing user interfaces (UI) and experiences (UX).
- 3D printing software: Programs such as Ultimaker Cura, PrusaSlicer, and Simplify3D are used to prepare 3D models for printing, optimizing layouts and settings for faster and more accurate results.
- Collaboration tools: Platforms like Zeplin or Figma streamline team collaboration by enabling real-time feedback and efficient design handoffs to developers.
- Simulation tools: Virtual prototyping software like COMSOL Multiphysics or ANSYS allows designers to test functional elements, stress points, and performance digitally.
By integrating these tools into the prototyping process, teams can speed up iterations, improve accuracy, and reduce overall development time.
Further reading
If you found this interesting, we discussed 2D to 3D digital transformation with Jonathan Bannister from DTCo to learn why ensuring an entire production process from conception to build should be recorded as 3D information.